Electric RC
- the Technology Behind the Revolution
Electric rc models really surged in popularity since the early 2000s, and this is particularly noticeable in radio control airplanes and helicopters and, more recently, drones.
RC surface vehicles (cars & boats etc.) have been powered by electric motors without problem for decades, but radio control aircraft have always had the serious issue of weight to contend with; keeping an rc aircraft as light as possible is of paramount importance if good flying performance is to be achieved.
In the past this has proved very difficult with electric rc aircraft, because lightweight high-capacity battery cells to power the motor and lightweight micro servos and receivers were just not available. Big and chunky components were largely the order of the day!
But thankfully an electronic revolution has been happening since the late 1990s which has seen mass-produced battery packs, electric motors, electronic speed controls (ESCs), servos and receivers become smaller, lighter, more powerful and very widely available - all adding up to electric rc aircraft improving greatly in performance, and becoming easier and cheaper to buy. Great news for us!
This article briefly talks about...
- Battery types.
- Battery charging.
- Cell ratings.
- Brushless motors.
- Speed control.
- Mini servos & receivers.
Electric RC Battery (cell)Types
The word battery is often used to describe what is in fact a single cell. For example, if your rc transmitter requires 8 AA batteries, it in fact requires 8 AA cells. Technically a battery is a collection of two or more cells but the battery/cell misunderstanding has become widely accepted and it's perfectly normal to say "8 AA batteries" instead of "8 AA cells".
Two types of cell can be used for electric rc applications - non-rechargeable and rechargeable. The non-rechargeable (alkaline) ones must be disposed of once their energy is depleted, whereas rechargeables can be used over and over, maybe up to 1000 times if they're good quality cells and are charged and discharged correctly.
Using disposable alkaline cells in a radio control model and transmitter is not uncommon, especially in cheaper models and electric rc toys, but rechargeable cells are a much more sensible option - and will cost you less in the long run.
The original rechargeable cells were Nickel Cadmium ones, abbreviated to NiCD or 'nicads'. These are rarely used nowadays and have been succeeded by Nickel Metal Hydride (NiMH) and Lithium-ion based cells (Li-Po, Li-Fe...).
NiCDs are the least powerful of the three and cadmium, the type of metal used inside the cell, is extremely toxic - these two reasons alone are enough not to use NiCD cells these days!
Nickel Metal Hydride cells (NiMH) have 3 or 4 times the capacity of an equivalent-sized NiCD and are commonly used in electric rc models, both in the model itself and in the transmitter.
NiMH cells don't suffer from the so-called memory effect that NiCDs do and so can be charged regardless of their present charge level, whereas nicads should always be fully discharged before being recharged to prevent cell damage.
The lithium-ion polymer battery packs (aka Li-Po, lipo or lipoly) are a more recent major development in rechargeable cell technology and these alone have drastically transformed the face of electric rc flight. They have a very high capacity relative to their size and weight, and deliver much longer run times and higher power than NiMH or NiCD packs.
In the relatively short time that Li-Po packs have been around, they've quickly become the standard choice for rc pilots the world over.
Disadvantages of Li-Po battery packs are that they can be a potential fire hazard if charged incorrectly and the cost is considerably more than their NiMH cousins, although this cost is falling all the time. But the advantages in performance of using a Li-Po battery pack in an electric rc aircraft far outweigh this extra cost.
High-end Li-Po powered electric rc airplanes (and helicopters) can now match the performance of glow plug powered aircraft in terms of speed and flight times. That was an impossible idea not that long ago!
Charging your Cells & Battery Packs
It's very important to pay close attention to the charging requirements of your rechargeable cells.
If you've purchased an RTF electric rc airplane or helicopter then the chances are that an appropriate charger is included in the box. If not, invest in a good quality peak detection charger. Such chargers prevent over-charging and the associated damage to the cells.
If in doubt speak with the person you are buying from and tell him/her exactly which cells you will be charging.
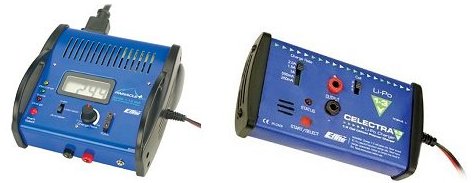
Above: on the outside there isn't much to differentiate between NiMH (left) and Li-Po (right) chargers, but using the correct one is so important. Good chargers will charge all cell types.
Charging NiMH cells is a straightforward process, so long as you take the time to calculate the optimum charging time given the capacity of your cells and the charger output. This is a simple calculation, the battery capacity in mAh (milliamp hour) is divided by the charge rate of the charger, in mA (milliamps). Charging information may also be displayed on the cells themselves - for example, "7h-110mA" tells you that the cell should be charged for 7 hours at a rate of 110mA.
Charging Li-Po packs is a different story altogether and it's imperative that you charge them with a charger meant for Li-Po cells. The charging algorithms are different for lithium polymer battery packs and packs can potentially explode when over-charged, creating a fireball - you don't want this happening! (Do a search for "Li-Po battery fire" on YouTube to see what can happen).
But although a lot of the horror stories you might read relate to when Li-Po technology was in its infancy and still being experimented with, there is a higher risk associated with them, compared to NiMH packs, and it's always a good idea to charge Li-Po packs under supervised conditions i.e. don't put a pack on charge and then leave the house.
A fireproof charging bag for Li-Po packs can be purchased from most hobby shops; they don't cost a lot and will give you some peace of mind.
Thankfully, li-po battery pack disasters don't happen too often and the technology has proven itself to be perfectly safe.
As well as the familiar capacity and voltage labelling, on Li-Po packs you may often see the words "Do not charge above 1C" as well. This means that the pack must not be charged at a rate that is greater than it's capacity.
For example, a 1000mAh battery should be charged at a maximum rate of 1000mA, or 1A. Charging the same pack at 800mA (0.8A) would be the same as charging at 0.8C. Charging a 2200mAh pack at 0.8C would mean charging it at 2200x0.8=1760mA, or 1.76A, and so on.
Charging a Li-Po pack above 1C greatly increases the risk of damage to the pack although it has to be said that as Li-Po technology is developing more and more packs that can tolerate a 'higher C charge' are becoming available.
'Trickle charging' is a term used to describe a method of very low-current continuous charging to compensate the cell's natural discharge rate, thus keeping the cell topped up so long as it is connected to the charger. Many fast battery chargers automatically switch over to trickle charging once the main fast-charge has completed, but this is only applicable to NiMH or lead acid cells and not Li-Po ones.
Capacities, Voltage & other Ratings
All cells and packs have a capacity and the value is expressed in milliampere-hours, often abbreviated to mAh.
Think of this capacity as "how much fuel is in the tank"; the higher the capacity, the more work the cell can do over a given time period or the longer the cell can work for. The mAh value represents, theoretically, how much current will flow from the cell over one hour eg a 600mAh cell will give 600 milliamps over one hour, or 1200 milliamps over half an hour, or 300mAh for two hours etc.
Logically, the longer you want to play between charges, the higher the capacity of the pack needs to be.
Ratings when Connecting Multiple Cells
When individual cells are connected together to make a battery pack there are two methods of connection - in parallel and in series.
By wiring cells together in parallel the positive terminals connect to positive terminals and negative to negative. The end result is an increase in total capacity but the voltage remains at the level of just one of the cells.
By wiring cells together in series the positive terminal of a cell is connected to its neighbouring negative terminal. This results in the total capacity staying at the level of each individual cell, but the overall voltage is increased to the value of all cells added together.
For example: 7 x 600mAh AAA NiMH cells wired in series to make up a small battery flight pack do not create a 4,200mAh flight pack - the pack's capacity stays at 600mAh but the voltage becomes 7 x 1.2V = 8.4V. Conversely, 7 x 600mAh AAA cells wired in parallel will result in a 4200mAh 1.2V pack.
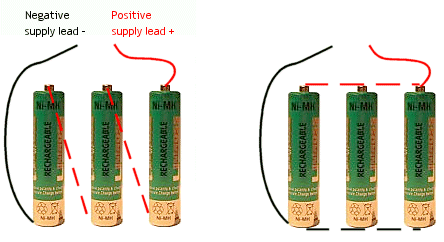
Above left: series wiring of cells compared to parallel wiring, right.
Battery packs for rc models have their cells connected in series, with the exception of larger Li-Po packs....
Li-Po Cell & Pack Ratings
Li-Po battery packs have a different rating system and can have cells wired in series, then wired in parallel to an identical set of cells. This gives the best of both worlds - the higher voltage from the cells wired in series plus the higher capacity from the two sets of cells being wired together in parallel. It's this combination that helps make Li-Po battery packs perform so well.
The nominal voltage of a single Li-Po cell is 3.7V, compared to the 1.2V of a NiMH cell, so Li-Po battery packs can be bought in increments of 3.7. For example, 3 cells connected in series will give a 11.1V pack, 4 cells a 14.8V pack and so on. The fully charged voltage of a Li-po cell is 4.2V, while their minimum safe voltage is generally accepted to be around 3V. Over-discharging Li-po cells causes serious damage to them.
Li-Po battery packs are rated with S, P and C values. For example a '3S' pack will have 3 cells wired in series, while a '3S-2P' pack will have those same serially-wired 3 cells connected in parallel to an identical 3 cells, hence the 3S-2P labelling; '3 series - 2 parallel'.
As well as the 'C' charging recommendations talked about earlier, 'C' values are also given to a Li-Po battery pack to determine the cell's discharge capability. Two ratings may be given on a pack, a continuous and burst rating; for example, a pack may be labeled as 2200mAh 15/25C which tells us that it can handle a continuous 33A discharge (2200x15/1000) or a burst of 55A (2200x25/1000). The 'industry standard' burst rate is a 15 second time limit.
The continuous C rating also lets us know how long the current draw can be sustained, theoretically. A 2200mAh 15C pack can deliver 33A for 1/15 of an hour, or 4 minutes while a 2200mAh 30C pack could deliver 66A for 1/30 of an hour, or just 2 minutes - lots of power, but no time to enjoy it! Of course, the reality is that higher rated packs will run for longer because you wouldn't be running them at their limits.
Brushless Electric RC Motors
At the forefront of the advance in electric rc modelling is the brushless motor.
Traditionally, electric powered rc models have used standard DC 'brushed' motors. In these, as part of the motor's operation, carbon brushes press against a spinning commutator and this causes friction. This unwanted but inevitable friction puts extra strain on the motor and makes the motor less efficient. Also, the brushes wear down with use and so need periodical replacement. These are the two big disadvantages with brushed motors.
While such motors do work well, a brushless motor uses electronic circuitry (in the ESC) and powerful Rare Earth magnets to do the job of the brush/commutator system. No revolving parts ever touch each other apart from the shaft and bearings. As a result there is no friction to speak of and therefore much greater efficiency, meaning a huge increase in power - brushless motors can be up to 300% more powerful than their brushed counterpart, and they also do away with the issue of periodical brush replacement.
There are two types of brushless motor used in radio control modelling; the inrunner motor and outrunner motor.
The inrunner motor is closer to a brushed motor in that the body remains stationary while the permanent magnets and shaft spin within the fixed stator. Inrunner motors, although much more powerful than brushed motors, are still limited in their torque and usually need gearing when used in a larger airplane or helicopter. Inrunners are suitable for smaller propeller sizes.
Outrunner brushless motors are different because the permanent magnets are attached to the inside of the motor casing, or 'can', and it's the can that rotates around the fixed stator. When you see an outrunner in operation you will see the outer can spinning. Outrunners generate more torque than inrunners and are very suitable for larger aircraft, and a gearbox is not normally necessary as the torque from the motor alone is sufficient.
Inrunner brushless motors, generally speaking, are more suited to swinging a smaller propeller at higher RPM whereas outrunners are more suited to swinging a larger prop at lower RPM.
As with most things electronic, brushless motors carry a rating system, in this case known as a kV rating. The kV value is the RPM (revs per minute) of the motor per each volt fed to it.
For example, a 900kV motor powered by a 12.6V Li-Po battery pack will give 900 x 12.6 = 11,340 RPM with no load. This is, like most things, more theoretical than anything else but gives a good indication of the motor's abilities and is a necessary part of motor selection for a particular electric rc aircraft.
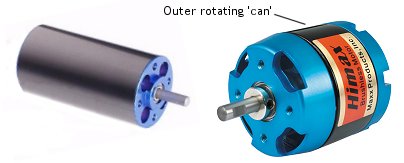
Above: the difference in appearance between an inrunner (left) and outrunner (right) brushless motor.
Speed Control
The speed of electric motors is controlled by speed controllers.
Traditional mechanically operated controllers have been replaced with much more effective electronic speed controllers (or electronic speed controls), or ESCs, which plug directly into the electric rc model's receiver throttle slot instead of being linked to a servo as a mechanical one needs to be.
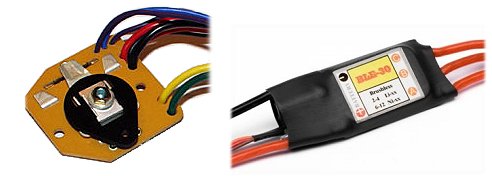
Above left: a traditional mechanical SC with necessary servo linkage,
compared to a modern ESC, right.
Whereas mechanical speed controllers varied the amount of volts entering the motor, modern ESCs allow the maximum volts through but at varying rates depending on the throttle stick position. The micro-processors, known as MOSFETs ( Metal Oxide Semiconductor Field-Effect Transistors ), in an ESC operate hundreds of times a second to let the current pass though them to deliver the required power to the motor.
ESCs for brushless motors are different to ones for brushed motors, technology-wise, and this is an important factor to consider when upgrading your model; never use a brushless motor with an ESC designed for a brushed motor. It's the complex circuitry in a brushless ESC that lets the ESC communicate with the motor and 'pulse' the electrical current from the battery pack to the motor in the correct sequences, for the motor to run properly.
ESC's are often programmable with features such as cell type, soft start, brake and low voltage cut off being common. This latter one (LVC) is important because it prevents the motor battery pack from being over discharged which could damage the cells, particularly with Li-Po cells.
When the low voltage cut-off point is reached the ESC will stop any further power to the motor, but will keep feeding power to the receiver and servos so you retain control of your plane, long enough to land safely.
This feed of current from the pack to the receiver and servos is done through a BEC, or battery eliminating circuit, which is an integral part of the ESC circuitry; it regulates a steady 5v or so from the motor battery pack to the radio components and thus negates the need for a separate receiver battery pack, unless the current draw from larger (multiple, digital...) servos requires a separate feed - such is often the case in larger, more complex rc aircraft.
Brushless electric motors combined with Li-Po battery packs and ESCs are the ultimate combination for power when it comes to electric rc.
Micro Servos & Receivers
Equally important as lightweight and powerful battery packs and motors, micro servos and receivers have also contributed to the advance of electric rc in a micro-sized big way! Such components can weigh only a few grams, yet can be as powerful and efficient as some larger, standard-size servos.
Digital micro servos are also becoming more commonplace and they offer more precise and instant control than their analogue cousins.
Micro servos and receivers are widely used in smaller electric rc airplanes, such as Park Flyers and indoor rc airplanes, and helicopters. However, in many RTF rc helicopters the receiver is usually combined with the ESC and gyro, making it a '3 in 1' electronic component.
Well hopefully this article has given you an insight in to the technology that's driving the electric rc flying hobby. As this great electronic revolution continues, it really is a question of "How small can we go?" and "How powerful can we get?"!
The components now seen in electric rc modelling really have drastically changed the face of the hobby, and we can only wonder how our radio control aircraft will be a few years from now...